Study of the steering of a wide span vehicle controlled by a local positioning system
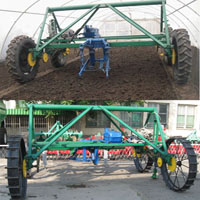
All claims expressed in this article are solely those of the authors and do not necessarily represent those of their affiliated organizations, or those of the publisher, the editors and the reviewers. Any product that may be evaluated in this article or claim that may be made by its manufacturer is not guaranteed or endorsed by the publisher.
Authors
Controlled traffic farming allows to minimize traffic-induced soil compaction by a permanent separation of the crop zone from the traffic lanes used by wide span tractors. The Authors developed an agricultural wide span vehicle equipped with a skid equipment for turning and an automatic driving system prototype based on a laser beam. The aim of this work was to study the kinematic conditions that control the steering of this machine. Furthermore, the accuracy and the maximum delay time of the signal transmission by the automatic driving system of the set-up was also assessed. In comparison with crawler tractors, the turning of the agricultural wide span vehicle needs a smaller difference in the moments applied to its right- and left-side wheels. For the predetermined accuracy of the beam position relative to the plant rows, ±ds = ±0.025 m, the accuracy of the direction of the laser beam at a distance S=200 m should not be more than ±0.07° and ±0.0014°, considering a run length of 1000 m. Furthermore, at a speed V=2.5 m s–1 a trajectory deviation φ≤5° requires a topmost delay time of the control signal of Δtmax=0.11 s is required.
How to Cite

This work is licensed under a Creative Commons Attribution-NonCommercial 4.0 International License.