Effect of the initial moisture content of the paddy drying operation for the small community
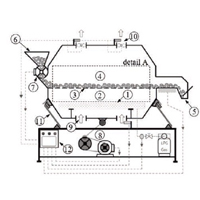
Published: 29 September 2020
Abstract Views: 2148
PDF: 796
HTML: 3842
HTML: 3842
Publisher's note
All claims expressed in this article are solely those of the authors and do not necessarily represent those of their affiliated organizations, or those of the publisher, the editors and the reviewers. Any product that may be evaluated in this article or claim that may be made by its manufacturer is not guaranteed or endorsed by the publisher.
All claims expressed in this article are solely those of the authors and do not necessarily represent those of their affiliated organizations, or those of the publisher, the editors and the reviewers. Any product that may be evaluated in this article or claim that may be made by its manufacturer is not guaranteed or endorsed by the publisher.
Similar Articles
- Andrea Galli, Cosimo Peruzzi, Fabiola Gangi, Daniele Masseroni, ArduHydro: a low-cost device for water level measurement and monitoring , Journal of Agricultural Engineering: Vol. 55 No. 1 (2024)
- Paolo Barge, Paolo Gay, Valentina Merlino, Cristina Tortia, Passive ultra high frequency radio frequency identification systems for single-item identification in food supply chains , Journal of Agricultural Engineering: Vol. 48 No. 1 (2017)
- Fabrizio Sarghini, Prospero Di Pierro, Antonio Veneruso, Paolo Masi, Scale-up analysis and critical issues of an experimental pilot plant for edible film production using agricultural waste processing , Journal of Agricultural Engineering: Vol. 43 No. 4 (2012)
- Federico Preti, Tommaso Letterio, Shallow landslide susceptibility assessment in a data-poor region of Guatemala (Comitancillo municipality) , Journal of Agricultural Engineering: Vol. 46 No. 3 (2015)
- Sara Cucchiaro, Laura Carretta, Paolo Nasta, Federico Cazorzi, Roberta Masin, Nunzio Romano, Paolo Tarolli, Multi-temporal geomorphometric analysis to assess soil erosion under different tillage practices: A methodological case study , Journal of Agricultural Engineering: Vol. 53 No. 1 (2022)
- Francisco Ayuga, Present and future of the numerical methods in buildings and infrastructures areas of biosystems engineering , Journal of Agricultural Engineering: Vol. 46 No. 1 (2015)
- Salvatore Benfratello, Costanza Di Stefano, Vito Ferro, Luigi Palizzolo, Testing mechanical characteristics of chestnut stakes used in bed sills for stream restoration , Journal of Agricultural Engineering: Vol. 48 No. 3 (2017)
- Giuliano Vox, Pierfrancesco Losito, Fabio Valente, Rinaldo Consoletti, Giacomo Scarascia-Mugnozza, Evelia Schettini, Cristoforo Marzocca, Francesco Corsi, A wireless telecommunications network for real-time monitoring of greenhouse microclimate , Journal of Agricultural Engineering: Vol. 45 No. 2 (2014)
- Johnny Moretto, Emanuel Rigon, Luca Mao, Lorenzo Picco, Fabio Delai, Mario Aristide Lenzi, Medium- and short-term channel and island evolution in a disturbed gravel bed river (Brenta River, Italy) , Journal of Agricultural Engineering: Vol. 43 No. 4 (2012)
- Xingbo Hu, Tian Xia, Leidong Yang, Fangming Wu, Ying Fan, Yinghong Tian, 3D modeling and volume measurement of bulk grains stored in large warehouses using bi-temporal multi-site terrestrial laser scanning data , Journal of Agricultural Engineering: Vol. 55 No. 1 (2024)
<< < 9 10 11 12 13 14 15 16 17 18 > >>
You may also start an advanced similarity search for this article.