Computational fluid dynamics simulation and optimisation of the threshing unit of buckwheat thresher for effective cleaning of the cleaning chamber
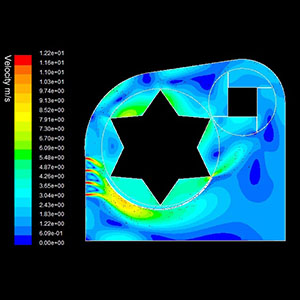
All claims expressed in this article are solely those of the authors and do not necessarily represent those of their affiliated organizations, or those of the publisher, the editors and the reviewers. Any product that may be evaluated in this article or claim that may be made by its manufacturer is not guaranteed or endorsed by the publisher.
Authors
Since a combined harvester’s grain-cleaning method depends on the pneumatic separation of grain and chaff, the airflow’s aerodynamic forces significantly affect cleaning efficiency. Based on buckwheat’s theoretical and mechanical properties, a new threshing drum with cleaning key parts was developed to reduce the variability of cleaning efficiency of buckwheat community threshers caused by inefficient threshing and accumulation of residue within the threshing system. This cleaning arrangement includes two wind speed inlets, each composed of four thin pipes of the same length as the threshing drum. The computational fluid dynamics modelling approach simulated the threshing and cleaning performance at different wind velocities within the threshing unit. The results showed that when the two inlets work simultaneously and adopt different wind speeds, i.e., 12 m/s and 15 m/s, the wind speed is higher than the critical value of the floating rate buckwheat kernel. Under this condition, the wind speed inlet area was increased, and the flow field velocity between the threshing drum and the concave grid plate ranged from 3.8 m/s-8.3 m/s. The flow velocity below the plate ranged from 7 m/s-15 m/s, higher than the floating speed of buckwheat kernels, which was the best choice. Based on these simulation results, a centrifugal fan was designed, which meets the buckwheat thresher’s cleaning performance.
How to Cite

This work is licensed under a Creative Commons Attribution-NonCommercial 4.0 International License.