Theoretical transmission analysis to optimise gearbox for a 2.6 kW automatic pepper transplanter
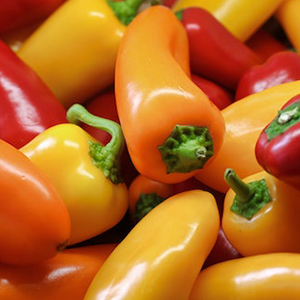
Published: 3 November 2022
Abstract Views: 1230
PDF: 323
Publisher's note
All claims expressed in this article are solely those of the authors and do not necessarily represent those of their affiliated organizations, or those of the publisher, the editors and the reviewers. Any product that may be evaluated in this article or claim that may be made by its manufacturer is not guaranteed or endorsed by the publisher.
All claims expressed in this article are solely those of the authors and do not necessarily represent those of their affiliated organizations, or those of the publisher, the editors and the reviewers. Any product that may be evaluated in this article or claim that may be made by its manufacturer is not guaranteed or endorsed by the publisher.
Similar Articles
- Roberto Deboli, Angela Calvo, Venerando Rapisarda, Christian Preti, Marco Inserillo, Vibration transmitted to operator’s back by machines with back-pack power unit: a case study on blower and spraying machines , Journal of Agricultural Engineering: Vol. 44 No. s2 (2013): Proceedings of the 10th Conference of the Italian Society of Agricultural Engineering
- Salvatore Faugno, Luisa del Piano, Mariano Crimaldi, Gennaro Ricciardiello, Maura Sannino, Mechanical oil extraction of Nicotiana tabacum L. seeds: analysis of main extraction parameters on oil yield , Journal of Agricultural Engineering: Vol. 47 No. 3 (2016)
- Damiano Coppolecchia, Davide Gardoni, Cecilia Baldini, Federica Borgonovo, Marcella Guarino, The influence on biogas production of three slurry-handling systems in dairy farms , Journal of Agricultural Engineering: Vol. 46 No. 1 (2015)
- Paolo Barge, Paolo Gay, Valentina Merlino, Cristina Tortia, UHF-RFID solutions for logistics units management in the food supply chain , Journal of Agricultural Engineering: Vol. 44 No. s2 (2013): Proceedings of the 10th Conference of the Italian Society of Agricultural Engineering
- Ahmed Shawky El-Sayed, Ibrahim Said Mosaad, Development of treated cardboard waste injection machine into the sandy soils , Journal of Agricultural Engineering: Vol. 53 No. 4 (2022)
- Gabriele Delogu, Lorenzo Boccia, Giuseppina Mari, Terraced landscapes: risk and liability , Journal of Agricultural Engineering: Early Access
- Yun Zhu, Shuwen Liu, Xiaojun Wu, Lianfeng Gao, Youyun Xu, Multi-class segmentation of navel orange surface defects based on improved DeepLabv3+ , Journal of Agricultural Engineering: Vol. 55 No. 2 (2024)
- Alessio Cappelli, Lucrezia Lupori, Enrico Cini, Should extra virgin olive oil production change the approach? A systematic review of challenges and opportunities to increase sustainability, productivity, and product quality , Journal of Agricultural Engineering: Vol. 54 No. 1 (2023)
- Xiong Bi, Hongchun Wang, Double-branch deep convolutional neural network-based rice leaf diseases recognition and classification , Journal of Agricultural Engineering: Vol. 55 No. 1 (2024)
- Fuhao Zhu, Jin Chen, Zhuohuai Guan, Yahui Zhu, Hao Shi, Kai Cheng, Development of a combined harvester navigation control system based on visual simultaneous localization and mapping-inertial guidance fusion , Journal of Agricultural Engineering: Vol. 55 No. 3 (2024)
<< < 33 34 35 36 37 38 39 40 41 42 > >>
You may also start an advanced similarity search for this article.