Airflow basin structure numerical optimisation analysis and suction nozzle characteristics experimental study of vacuum-vibration tray precision seeder
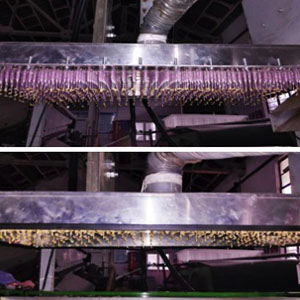
All claims expressed in this article are solely those of the authors and do not necessarily represent those of their affiliated organizations, or those of the publisher, the editors and the reviewers. Any product that may be evaluated in this article or claim that may be made by its manufacturer is not guaranteed or endorsed by the publisher.
Authors
The stable and uniformly distributed airflow field can effectively improve the seed suction effect and seed-carrying stability of the pneumatic seeder. With this end in view, this paper optimised the airflow basin structure of the vacuum-vibration tray precision seeder based on the computational fluid dynamics (CFD) simulation technology. The results show that the airflow field is relatively stable and well-distributed when the chamber height is 50 mm, and the outlet tube diameter is 65 mm. In addition, the thickness of the base plate with suction holes should be less than 5 mm, and the needle suction nozzle guide should be greater than 15 mm, according to the numerical analysis results. Based on the above study, the seeding characteristics of the needle-type suction nozzle and the plate-type suction nozzle were further explored to determine the type of nozzle more suitable for a rectangular sucker. Through various experimental designs, the significant influencing factors of the two suction nozzles, their appropriate working ranges, and the optimal combination of working parameters were determined in turn. The needle suction nozzle requires a lower suction height and less grain dispersion, according to the experimental results, while the plate suction nozzle is just the opposite; it allows a certain suction height to be maintained with the seeds and requires high dispersion of grain. In general, the plate suction nozzle can obtain better seeding performance and is a more favourable nozzle for the vacuum-vibration tray precision seeder.
How to Cite

This work is licensed under a Creative Commons Attribution-NonCommercial 4.0 International License.