Cassava stalk detection for a cassava harvesting robot based on YOLO v4 and Mask R-CNN
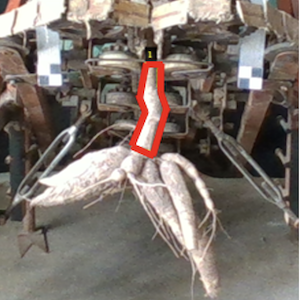
All claims expressed in this article are solely those of the authors and do not necessarily represent those of their affiliated organizations, or those of the publisher, the editors and the reviewers. Any product that may be evaluated in this article or claim that may be made by its manufacturer is not guaranteed or endorsed by the publisher.
Authors
The quality of fresh cassava roots can be increased through the use of precision equipment. As a first step towards developing an automatic cassava root cutting system, this study demonstrates the use of a computer vision system with deep learning for cassava stalk detection. An RGB image of a cassava tree mounted on a cassava-pulling machine was captured, and the YOLO v4 model and two Mask R-CNN models with ResNet 101 and ResNet 50 base architectures were employed to train the weights to predict the position of the cassava stalk. One hundred test images of stalks of various shapes and sizes were used to determine the grasping point and inclination, and the results from manual annotation were compared with the predicted results. Regarding localisation, Mask R-CNN with ResNet 101 gave a significantly higher performance than the other models, with an F1 score and a mean IoU of 0.81 and 0.70, respectively. YOLO v4 showed the highest correlation for the x- and y-coordinates for the prediction of the grasping point, with values for R2 of 0.89 and 0.53, respectively. For inclination prediction, Mask R-CNN with ResNet 101 and Mask R-CNN with ResNet 50 gave the same level of correlation, with values for R2 of 0.50 and 0.61, respectively. These results were acceptable for use as design criteria for developing a cassava rootcutting robot.
Supporting Agencies
Khon Kaen UniversityHow to Cite

This work is licensed under a Creative Commons Attribution-NonCommercial 4.0 International License.