Structural design, modeling and simulation analysis of a cage broiler inspection robot
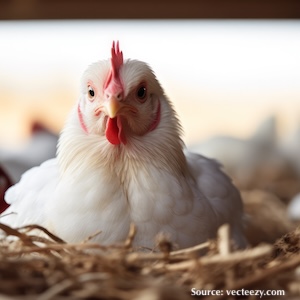
Published: 7 April 2025
Abstract Views: 205
PDF: 21
Publisher's note
All claims expressed in this article are solely those of the authors and do not necessarily represent those of their affiliated organizations, or those of the publisher, the editors and the reviewers. Any product that may be evaluated in this article or claim that may be made by its manufacturer is not guaranteed or endorsed by the publisher.
All claims expressed in this article are solely those of the authors and do not necessarily represent those of their affiliated organizations, or those of the publisher, the editors and the reviewers. Any product that may be evaluated in this article or claim that may be made by its manufacturer is not guaranteed or endorsed by the publisher.
Similar Articles
- Dimas Firmanda Al Riza, Naoshi Kondo, Pasquale Catalano, Ferruccio Giametta, A preliminary study on the potential of front face fluorescence spectroscopy for Italian mono-cultivar extra virgin olive oil discrimination , Journal of Agricultural Engineering: Vol. 50 No. 1 (2019)
- Fabrizio Mazzetto, Aldo Calcante, Aira Mena, COMPARING COMMERCIAL OPTICAL SENSORS FOR CROP MONITORING TASKS IN PRECISION VITICULTURE , Journal of Agricultural Engineering: Vol. 40 No. 1 (2009)
- Vincenzo Bagarello, Costanza Di Stefano, Vito Ferro, Giordano Giuseppe, Massimo Iovino, A PEDOTRANSFER FUNCTION FOR ESTIMATING THE SOIL ERODIBILITY FACTOR IN SICILY , Journal of Agricultural Engineering: Vol. 40 No. 3 (2009)
- Vito Ferro, Ismail Aydin, Deducing the stage-discharge relationship for contracted weirs by the outflow theory of Malcherek , Journal of Agricultural Engineering: Vol. 50 No. 2 (2019)
- Francesco Barreca, Pasquale Praticò, Environmental indoor thermal control of extra virgin olive oil storage room with phase change materials , Journal of Agricultural Engineering: Vol. 50 No. 4 (2019)
- Enrica Santolini, Alberto Barbaresi, Daniele Torreggiani, Patrizia Tassinari, Numerical simulations for the optimisation of ventilation system designed for wine cellars , Journal of Agricultural Engineering: Vol. 50 No. 4 (2019)
- Pietro Catania, Mariangela Vallone, Diego Planeta, Felice Pipitone, ANALYSIS OF THE FILTRATION EFFICIENCY OF WHITE WINES USING DIFFERENT FILTER AIDS , Journal of Agricultural Engineering: Vol. 41 No. 1 (2010)
- Edwin Andrés Villagrán, Carlos Ricardo Bojacá, Effects of surrounding objects on the thermal performance of passively ventilated greenhouses , Journal of Agricultural Engineering: Vol. 50 No. 1 (2019)
- Giuseppe Toscano, Fabrizio Corinaldesi, ASH FUSIBILITY CHARACTERISTICS OF SOME BIOMASS FEEDSTOCKS AND EXAMINATION OF THE EFFECTS OF INORGANIC ADDITIVES , Journal of Agricultural Engineering: Vol. 41 No. 2 (2010)
- Angelo Fabbri, Chiara Cevoli, Florina Aurelia Silaghi, Adriano Guarnieri, NUMERICAL SIMULATION OF PHYSICAL SYSTEMS IN AGRI-FOOD ENGINEERING , Journal of Agricultural Engineering: Vol. 42 No. 4 (2011)
<< < 39 40 41 42 43 44 45 46 47 48 > >>
You may also start an advanced similarity search for this article.